MIT Libraries home DSpace@MIT
- DSpace@MIT Home
- MIT Libraries
- Doctoral Theses

Developing highly efficient lead halide perovskite solar cells
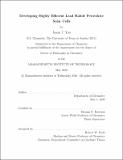
Other Contributors
Terms of use, description, date issued, collections.
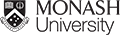
File(s) under embargo
until file(s) become available
The Upscaled Fabrication and Encapsulation of Perovskite Solar Cells
Campus location, principal supervisor, additional supervisor 1, year of award, department, school or centre, additional institution or organisation, degree type, usage metrics.
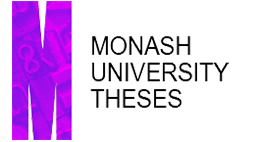
- Photovoltaic devices (solar cells)
- Photovoltaic power systems
- Oxford Thesis Collection
- Climate Research Collection
- CC0 version of this metadata
Perovskite materials for multi-junction solar cell applications
The work presented in this thesis will describe studies on organic-inorganic perovskite materials when being used in tandem and multi-junction solar cell architectures. Perovskite solar cells (PSC) have recently emerged as a viable absorber material for photovoltaic applications, owing to its remarkable optoelectronic properties along with its ease of fabrication. These attributes have led to a rapid progress in device performance, where over the last few years, perovskite solar cells have...
Email this record
Please enter the email address that the record information will be sent to.
Please add any additional information to be included within the email.
Cite this record
Chicago style, access document.
- McMeekin - 2018 - Perovskite Materials for Multi-Junction Sola... (pdf, 7.3MB)
Why is the content I wish to access not available via ORA?
Content may be unavailable for the following four reasons.
- Version unsuitable We have not obtained a suitable full-text for a given research output. See the versions advice for more information.
- Recently completed Sometimes content is held in ORA but is unavailable for a fixed period of time to comply with the policies and wishes of rights holders.
- Permissions All content made available in ORA should comply with relevant rights, such as copyright. See the copyright guide for more information.
- Clearance Some thesis volumes scanned as part of the digitisation scheme funded by Dr Leonard Polonsky are currently unavailable due to sensitive material or uncleared third-party copyright content. We are attempting to contact authors whose theses are affected.
Alternative access to the full-text
Request a copy.
We require your email address in order to let you know the outcome of your request.
Provide a statement outlining the basis of your request for the information of the author.
Please note any files released to you as part of your request are subject to the terms and conditions of use for the Oxford University Research Archive unless explicitly stated otherwise by the author.
Contributors
Bibliographic details, item description, related items, terms of use, views and downloads.
If you are the owner of this record, you can report an update to it here: Report update to this record
Report an update
We require your email address in order to let you know the outcome of your enquiry.

As a bona fide Library user, I declare that:
- I will abide by the rules and legal ordinances governing copyright regarding the use of the Database.
- I will use the Database for the purpose of my research or private study only and not for circulation or further reproduction or any other purpose.
- I agree to indemnify and hold the University harmless from and against any loss, damage, cost, liability or expenses arising from copyright infringement or unauthorized usage.
By downloading any item(s) listed above, you acknowledge that you have read and understood the copyright undertaking as stated above, and agree to be bound by all of its terms.
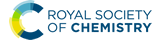
Carbon-based electrodes for perovskite solar cells

First published on 16th July 2021
The cost-effective processability and high stability of carbon-based perovskite solar cells (C-PSCs) have shown great potential to positively devote to the development of large-scale production processes. However, there are certain critical issues such as inferior performance and poor interface contact between perovskites and carbon electrodes, which have to be resolved first. The review shows that three main carbon materials, namely, carbon black, graphenes and carbon nanotubes display high photoelectric conversion efficiencies when being mixedly used as rigid electrodes and show excellent robustness in mechanical deformation as flexible carbon electrodes in carbon-based perovskite solar cells. Moreover, the specific development of and the comparison among three primary types of C-PSCs, namely, meso C-PSCs, embedment C-PSCs and paintable PSCs are emphasized. Furthermore, this work discusses the latest progress of C-PSC interface engineering from four aspects, namely, energy alignment, hysteresis effect, interface passivation and built-in electric field, and the differences among them are explained. Finally, further challenges and perspectives of C-PSCs are outlined. This work will be a profound influence and guidance on the significance of C-PSCs in commercialization.

1. Introduction
The metal electrode here is usually gold (Au), silver (Ag) or other highly conductive metals, but the metal layer is formed in a vacuum environment for thermal evaporation coating with high energy consumption, which severely hinders large-scale production and commercialization of PSCs. 20–24 From the perspective of work-function ( W f ), carbon materials ( W f ∼ −5.0 eV) have the potential to replace Au ( W f ∼ −5.1 eV) as the black electrode of the device. Carbon materials have the advantages of abundant sources, high electrochemical stability, and hole extraction, and these advantages are unavailable for metal electrodes. Therefore, the manufacturing process of carbon-based structures is simplified because of the lack of the hole transport layer. In addition, the specific hydrophobicity of the carbon material structure can also significantly enhance the stability of the solar cells. As illustrated in Fig. 1(a) , the traditional M-PSCs consist of five layers (Au, hole transport layer (HTL), light-absorbing, electron transport layer (ETL), fluorine-doped tin oxide (FTO)). 19 Then, the HTL was removed and the Au electrode was replaced with the carbon electrode, as shown in Fig. 1(b) . 19 In M-PSCs, the interaction between the perovskite film and the ETL determines the electron quasi-Fermi level ( E fn ), while the interaction between the perovskite film and the HTL determines the hole quasi-Fermi level ( E fp ) ( Fig. 1(c) ). 19 When removing the HTL, the interaction between the perovskite/carbon electrode predominantly determines the E fp value in carbon-based perovskite solar cells (C-PSCs), which will uplift the E fp position thanks to the higher Femi level of carbon materials than the highest occupied molecular orbital (HOMO) of the HTL ( Fig. 1(d) ). 19 Consequently, it is the premise that improving the V OC and PCE of C-PSCs is to reduce the Femi level of carbon materials.
Utilizing carbon black/graphite as an anode in PSCs, a PCE of 6.6% was first achieved. 25 After that, low-temperature cured carbon electrodes for PSCs were fabricated, which were developed as substitutes for noble metal electrodes in HTL-free PSCs. This carbon black electrode had achieved a PCE of 8.31%, which reached 9% by optimizing the conditions (doctor-blading technique). 25,26 In addition, a novel preparation of a low-temperature carbon black electrode for HTL-free PSCs had been developed under high relative humidity, and the black electrode had a small sheet resistance and a good interfacial contact with the substrate. 27 Subsequently, a room-temperature solvent-exchange method was developed to fabricate self-adhesive macroporous carbon electrodes. 28 A PCE up to 19.2% was achieved, which was the best efficiency for C-PSCs. The typical PCE improvement of C-PSCs along with years is shown in Fig. 2 . It can be seen that C-PSCs doped with other materials exhibit superior efficiency, on account that the dopant can change the conductivity and W f of the black electrode. 29–34
Carbon electrode materials were fabricated by two main deposition methods. The first method required high temperatures (400–500 °C). 19 Mesoporous carbon was deposited at the top of the insulating layer by screen printing or doctor-blading technology, and subsequently sintered. The insulating layer had the role of preventing the interface contact between the transparent and the rear electrode, and avoided photocurrent loss. Another strategy was layer-by-layer deposition, 19 thanks to the development of low-temperature carbon electrodes, which first formed perovskite films and then screen-printed or doctor-bladed carbon films on the perovskite layer or HTL. The current carbon electrode materials mainly include carbon black, graphenes and carbon nanotubes. Fig. 3(a) and (b) indicate that the PCE of M-PSCs was higher than that of C-PSCs, due to which the smooth surface of the Au electrode reflected incident light and caused the light-absorbing layer to absorb repeatedly. 35 In addition, the cross-sectional scanning electron microscopic (SEM) image of the obtained device is displayed in Fig. 3(c) and (d) . 36,37 Hence, the low-cost and low-temperature carbon black electrode had a great potential in massive flexible manufacturing of PSCs. Recently, three carbon materials have been explored to carbon electrodes such as carbon black, graphenes, and carbon nanotubes. 38–47 However, the carbon electrode still exhibits low conductivity, carrier recombination, poor interface contact, etc.
In this review, we focus on the major progress of C-PSCs in recent years, including the development of carbon-based materials, their preparation and new strategies to improve device structures. The following content was mainly composed of three parts: (I) the influences of the proportions of the three carbon materials (carbon black, graphenes, and carbon nanotubes) on the PCE are summarized; (II) the preparation methods of meso C-PSCs, embedment C-PSCs and paintable C-PSCs were described in detail, and their performance was emphasized and (III) starting from several aspects such as energy alignment, hysteresis effect, passivation of defects and built-in electric field, a broad overview of the interface engineering development of C-PSCs was carried out. Finally, the challenges and potentials of C-PSCs were summarized. We envision that this work will inspire researchers to employ the remarkable stability, low cost and hydrophobic properties of carbon materials to highly efficient and stable C-PSCs.
2. Carbon-based electrode materials in PSCs
2.1 carbon black.
Ku et al. used carbon black/graphite as the rear electrode of PSCs for the first time. 25 Then, Wei et al. utilized pure carbon black as the rear electrode for C-PSCs by collecting candle soot. 56 The structure of this carbon black was highly porous. In addition, the carbon electrode was printed on the pre-fabricated perovskite film during device preparation. Finally, the cell achieved a PCE of 2.6% because of the low conductivity of this carbon black. After that, they determined to employ commercial carbon black as the rear electrode, and the PCE of the device was greatly boosted which eventually reached 11.0%. 56 Huang et al. had also done related research. 57 It was necessary to first use methylammonium iodide (MAI) and carbon black to form carbon ink, resulting from the small size of carbon black, then they used inkjet printing technology to deposit carbon electrodes. When carbon ink was placed on the PbI 2 precursor layer, MAI reacted with PbI 2 in the ink and crystallized to a cubic perovskite phase, thus immobilizing and embedding carbon black to produce carbon electrons. It enhanced the back contact in the C-PSCs, resulting in the acceleration of carrier migration and reduced charge recombination. As a result, a PCE of 11.6% was achieved. 57
Recently, Gong et al. have introduced an intermediate layer of carbon black between the perovskite film and the carbon rear electrode. 48 The device was fabricated with the structure of the perovskite/carbon black/carbon electrode, where carbon black was employed to facilitate the hole extraction. They adopted a one-step spin-coating method with a preheating process for a high-quality perovskite film. 58–62 The configuration and band alignment of the device are illustrated in Fig. 4(c) and (d) . 48 Fig. 4(e) depicts the manufacture procedures of the perovskite layer, carbon black interlayer and carbon rear electrode. Obviously, the carbon black interlayer played a role of transition layer between perovskite and carbon rear the electrode, which accelerated hole extraction. It improved the extraction efficiency of holes because of the larger contact area and proper energy band arrangement in the interface perovskite/carbon electrode. As a result, the device achieved a recorded PCE of 13.13%. 48 Chu et al. designed a new type of carbon rear electrode with nanoscale carbon black and carbon fiber to improve the perovskite/carbon interface. 63 HTL-free PSCs were obtained by using double-layer carbon electrodes (coherent layer and conductive layer), thereby increasing the PCE to 14.1%. 63
2.2 Graphene
In 2015, You et al. applied graphene as a transparent rear electrode in the inverted PSCs for the first time. 73 The front electrode (FTO side) and the rear electrode (graphene side) were irradiated under 1 sun illumination, and the PCE were 12.02% and 11.6%, respectively. Graphene was widely used in inverted PSCs and replaced transparent conductive oxide (TCO) as the front electrode. 74 By using graphene transparent anodes and organic hole transport materials poly(3,4-ethylenedioxythiophene):poly(styrenesulfonate) (PEDOT:PSS), high-efficiency TCO-free PSCs were prepared. By adding MoO 3 and optimizing the thickness of the MoO 3 layer between the graphene anode and PEDOT:PSS, the highest PCE of 17.1% was obtained. Simultaneously, the PCE of the device with ITO transparent electrode was 18.8%. 74
These studies found that PCE vitally depended on the number of graphene layers. 74–76 The performance of the two-layer graphene device was the best and achieved the PCE with 12.37% certified value, while the PCE of the single-layer assembled device was 9.18%. 77 Nevertheless, the increased graphene layers resulted in deterioration of PCE (PCE for three and four layers were 11.45% and 11.27%, respectively). 77 A large quantity of layers reduced the transmittance of electrodes, and resulted in a decrease in quantities of photons reaching the absorber layer. In 2019, by Zhang et al. showed that graphene-based PSCs (G-PSCs) exhibit a PCE of 18.65%. 66 The optimized unpackaged device kept 90% of its initial PCE after aging for 1000 hours at a high temperature of 85 °C. Fig. 5(g) shows the SEM image of the G-PSC structure.
2.3 Carbon nanotubes
Furthermore, the mechanical property of CNTs was proved to be extremely beneficial for the exploitation of flexible PSCs. 88,89 Compared with the high treatment temperature of the carbon black/graphite composite electrode (above 450 °C), CNT films could be integrated into PSCs without any sintering, since remarkable optical characteristic and flexibility CNTs were very prospective in flexible PSC electrode materials. Luo et al. reported a cross-stacked carbon nanotube (CSCNT) film, 78 and later used an SnO 2 -coated carbon nanotube (SnO 2 @CSCNT) film as the electrode in flexible inverted PSCs in their work. 89 Compared with devices without SnO 2 coating, flexible inverted PSCs with SnO 2 @CSCNT cathodes had significantly improved photovoltaic performance. The results indicated that SnO 2 @CSCNT was a promising cathode material for long-term PSC operation. The typical SEM image of the CSCNT film is shown in Fig. 6(b) .
Jeon et al. developed a vapor doping method based on ex situ triflic acid (TFMS), which minimized the interaction with t-BP and shown the maximum doping effect. 79 In the case of traditional M-PSCs, an increase in the concentration of 2,2,7,7-tetrakis( N , N -di- p -methoxyphenylamine)-9,90-spirobifluorene (Spiro-MeOTAD) in HTL would decrease the PCE ( Fig. 6(c) ). It was in that the increase in HTL concentration resulted in a thicker Spiro-MeOTAD layer, causing a decrease in the hole transport capacity and vice versa . 79 However, it did not happen in the case of CNT lamination PSCs, as CNTs had already extracted holes in the interface before Spiro-MeOTAD restricted hole extraction ( Fig. 6(d) ). Combined the optimized carbon nanotubes and Spiro-MeOTAD ( Fig. 6(e) ), the best PCE of C-PSCs was higher than that of M-PSCs and reached 18.8% ( Fig. 6(f) ). 79 This was due to the superior hole selectivity of carbon nanotubes and the improvement of electrical conductivity by doping TFMS.
In conclusion, from a view of the application, the performance of graphene as a transparent electrode is the best due to good conductivity, high flexibility and light transmittance. 74 Carbon nanotubes are suitable to be counter electrodes because of their unique structure to promote hole extraction, 90 while carbon black can increase the pores of carbon paste, promote charge transfer and improve interface contact. 48 Therefore, it is reasonable to believe that if the carbon materials will be utilized as the basic electrode material, the PCE will possibly catch up with that of conventional M-PSCs.
3. Three types of C-PSC progress
3.1 meso c-pscs.
In the initial study of meso C-PSCs, the solution of PbI 2 and MAI was employed to the device via a one-step deposition technique, which achieved a PCE with 6.6%. 25 The inferior performance was due to the poor infiltration of the perovskite precursor solution in the device. To improve solution infiltration, Xu et al. applied an ordered porous carbon material as the carbon electrode, which boosted the solution infiltration and lightly increased the PCE to 7%. 113 As illustrated in Fig. 7(c) , the photocurrent density–voltage characteristic ( J – V ) curve of meso C-PSCs was plotted using OG-15, OG-16 and CG as counter electrodes, respectively. 113 Fig. 7(d) and (e) represent the assembled framework C-FDU-15 and C-FDU-16, respectively. 113 Fig. 7(f) shows the TEM image of C-FDU-15 seen in the (110) direction, and Fig. 7(g) shows the TEM image of C-FDU-16 viewed from the same direction. 113 A two-step technique was also explored for meso C-PSCs by Han's group, 111 which involved pre-deposition of PbI 2 , and then reached reaction in MAI solution to generate MAPbI 3 . By employing the TiO 2 nanosheet as the ETL, the meso C-PSCs exhibited the best PCE of 10.6%, 111 which enhanced to 11.6% after altering the graphite size and thickness of the carbon counter electrode. 112 Baranwal et al. evaluated the stability of the PCE of meso C-PSCs. 114 The results indicated that the efficiency of the encapsulated meso C-PSCs was not almost degraded at 100 °C, which indicated that the high thermal stability of the device had a chance to be achieved. Although the thick carbon layer could play a role in reducing the perovskite layer from being affected by moisture degradation, it must also avoid direct exposure of the rear electrode. There were two kinds of sealing positions of the device, as illustrated in Fig. 7(h) and (i) . These results indicated that meso C-PSCs had the opportunity to achieve high-efficiency PSCs. 114
3.2 Embedment C-PSCs
Carbon black was often used in the work of embedment of C-PSCs. However, the poor connectivity of carbon black would lead to an inferior interfacial contact. The addition of other adhesives would increase the connectivity, but prevent the infiltration of the solution and inhibit the conversion of PbI 2 into MAPbI 3 . In order to solve this issue, the bonding properties of other carbon materials (carbon black, graphite and MWCNTs) were compared. Finally, it was concluded that the FF values of the three carbon materials were very different, in the order of graphite (0.64) < carbon black (0.65) < MWCNTs (0.75). 64
In 2019, Yang et al. reported embedment C-PSCs based on carbon nanotubes. Carbon nanotubes were coated on PbI 2 and then immersed in CH 3 NH 3 I solution for 12 h to form a CH 3 NH 3 PbI 3 perovskite layer. Finally, the prepared CH 3 NH 3 PbI 3 perovskite layer was annealed on a hot plate at 100 °C for 10 min to obtain a complete device. On the basis of this device, they added a ferroelectric oxide (PbTiO 3 ) between the ETL and the perovskite layer. The PbTiO 3 was formed on TiO 2 by coating TiO 2 with (Pb(OAc) 2 ·3H 2 O), and then annealing at 450 °C for 1 h. The PbTiO 3 could provide a larger internal electric field and inhibit the non-radiative recombination of carriers, and the corresponding PCE of device reached 16.37%.
3.3 Paintable C-PSCs
Zhang et al. applied a commercial carbon paste to paintable C-PSCs for the first time. 26 By systematically altering the thickness of the TiO 2 layer, the device obtained a PCE of 8.3%. In the beginning, the PCE of paintable C-PSCs was very low, but the simplest manufacturing process continued to inspire researchers to enhance the efficiency of the device. By optimizing the ratio of paint composition (carbon black and graphite), Yang et al. obtained a PCE of 10.2%. 128 In 2015, Wei et al. developed a flexible carbon paste printing on the LHP layer, which effectively avoided the negative influence of the solvent on the perovskite film, and finally obtained a PCE with 13.5%. 52
The research on the stability of paintable C-PSCs had been reported by literatures. 129,130 Wei et al. compared the effects of epoxy resin and Ag coating on the carbon electrode. 131 Epoxy resin was a kind of polymer in carbon paste and had superior water resistance. Compared with the pure carbon electrode, carbon paste as the electrode had a better hydrophobicity. The Ag coating could enhance the hydrophobicity. In addition, the Ag coating could also improve the conductivity of the carbon electrode. Because perovskite was easily degraded by moisture, hydrophobicity was very important. 131 This was proved by the environmental stability measurement. The device with epoxy resin had higher stability, and the Ag coating acted like the icing on the cake. 131
Zhang et al. exploited a self-adhesive macroporous carbon film by solvent exchange at room temperature. 28 In the previous process, the solvent in the carbon paste was removed by high-temperature volatilization, which seriously affected the flexibility and porosity of the carbon paste, labeled as C1. It was found that ethanol could effectively inhibit the curing of carbon paste during solvent exchange. Fig. 9(c) depicts the microscopic curing mechanism of carbon paste. 28 After the exchange process was completed, the carbon film fell off from the glass substrate and formed a self-supporting film, which was marked C2. This method can avoid high-temperature curing. Fig. 9(d) shows the SEM images of devices with C1 and C2 as black electrodes, respectively. 28 It was found that there was a large gap between C1 and the Spiro-MeOTAD layer, while there was almost no gap between C2 and the Spiro-MeOTAD layer, and hence, it had a better interfacial contact.
There were obvious differences among the three kinds of C-PSCs in the preparation process, especially in the preparation and deposition of carbon paste. The multi-layer mesoporous structure in meso C-PSCs limited the complete conversion of pre-deposited PbI 2 . 99–101,132 In the preparation of embedment C-PSCs, the TiO 2 layer and the carbon layer should be deposited separately by a two-step method when pre-depositing PbI 2 . 71,133–135 For paintable C-PSCs, it was deposited layer by layer. No matter it was the one-step method, the two-step method or other development methods, it could be applied. Due to its superior stability, low cost of production and large market potential, C-PSCs had become a critical part of the PSC field. 136–141 Table 3 lists the fabrication parameters of different techniques. It can be seen that the PCE of paintable C-PSCs exhibited the best.
Although C-PSC-related research had achieved excellent results, the inferior interface contact between the perovskite film and the carbon electrode remained to be solved.
4. Interface engineering of C-PSCs
4.1 energy alignment.
In 2019, Wang et al. employed a kind of high conductivity and low-temperature carbon paint to paintable C-PSCs. 108 The carbon paint had good perovskite compatibility and conductivity, and the final PCE was 11.7%. 108 The interfacial contact was improved and hole extraction was increased by introducing hole transport layer (3,4-ethylenedioxythiophene:polystyrene sulfonate (PEDOT:PSS)). Fig. 10(c) shows the fabrication process of this device. The cross-sectional scanning electron microscopic image of cryogenic C-PSCs is shown in Fig. 10 (d). It was worth noting that it was difficult to match PEDOT:PSS ( W f ∼ 4.8 eV) and carbon ( W f ∼ 4.8–5.0 eV), as shown in Fig. 10(e) . Therefore, the close contact between perovskite and carbon electrode accelerated the hole collection and achieved 14.55% PCE. 108
4.2 Hysteresis effect
The HTL-free C-PSCs not only reduced the cost but also increased the stability. However, the performance of the TiO 2 -based ETL was unstable due to the hysteresis phenomenon. 173,174 Therefore, the non-hysteresis phenomenon C 60 was chosen as the ETL, to form the All-C-PSCs. Meng et al. fabricated a FTO/C 60 /MAPbI 3 /carbon device structure, in which a PCE of C 60 -based device was 15.38%, while that of TiO 2 -based device was only 12.06%. 30 The cross-sectional SEM image of the All-C-PSCs is shown in Fig. 11(a) . The C 60 value effectively improved the electron extraction, suppressed the charge recombination and reduced the sub-band gap state at the interface with the perovskite. Furthermore, the All-C-PSCs prevented moisture from entering the perovskite layer and had superior operation stability in a humid environment. Graphene was further used as a transparent conductive electrode to make it real All-C-PSCs and finally achieved 13.93% PCE. The high performance of the All-C-PSCs came from the bonding flexibility and electronic versatility of carbon materials. 175–179 The SEM image of the All-C-PSCs is shown in Fig. 11(b) , where the thickness of the carbon layer was about 20 μm, which prevented moisture from infiltration into the perovskite. 30 Fig. 11(c) shows the J – V curve of the All-C-PSCs based on graphene transparent electrodes. The reverse scan was 0.35% higher than the PCE of the forward scan. 30 Fig. 11(d) shows the reverse and forward scan J – V curves of C 60 and TiO 2 ETL, under the condition of AM 1.5G 100 mW cm −2 . 30 It can be seen that the TiO 2 -based C-PSCs showed an obvious hysteresis. When replaced by C 60 , the efficiency of electron extraction was enhanced and the J – V hysteresis was eliminated. 30
As shown in Fig. 11(h)–(j) , there was almost no difference between the forward and reverse directions of the J – V curves of carbon black and MWCNTs at the same scanning rate, indicating that the hysteresis of the two materials was very small. However, there was an obvious difference in the J – V curve of graphite, which mean that there was a large hysteresis phenomenon in graphite. Because the three kinds of carbon materials had similar cell configuration and device structure, it was considered that the effect of hole transfer on the hysteresis effect was different if the contact between carbon electrode and perovskite interface was different. 127 Through the study of the hysteresis effect of three kinds of carbon materials, MWCNT was expected to prepare high-efficiency C-PSCs without hysteresis. 127
4.3 Passivation defect
Yang et al. applied a polyethyleneimine-functionalized carbon nanotube (PEI/CNT) to the interface between the perovskite layer and the carbon electrode to improve the interface contact. 181 PEI molecules also had the effect of passivating interface defects. 181 It was found that PEI molecules were anchored on the perovskite framework by amino groups via the coordination interaction between –NH 2 (–NH–) and Pb 2+ or the hydrogen bond between H atoms in –NH 2 (–NH–) and I − , thereupon passivating the surface trap state in CsPbI 3 . 181 Due to the improvement of the contact between the perovskite/carbon interface, the charge transfer was accelerated. C-PSCs finally obtained 10.55% PCE and 0.71 FF. 181 Fig. 12(g) shows the specific structure of the device, and the existence of the PEI/CNT bridge could be observed. 181 During the preparation of C-PSCs, the PEI/CNT bridge was deposited on the perovskite/carbon electrode interface and partially infiltrated in the perovskite layer, as shown in Fig. 12(h) . 181 CNTs were first oxidized by mixed acids (sulfuric acid and nitric acid), and then carboxyl groups were introduced into the surface of CNTs. Finally, PEI molecules were connected to CNTs by the dehydration reaction between carboxyl and amino groups. 185 Hence, the PEI/CNT interface bridging method was expected to prepare efficient and stable C-PSCs.
4.4 Build-in electric field
Lee et al. revealed that increasing the difference in W f between the carbon electrode and the perovskite layer could facilitate the driving force of carrier migration, which indicated that the built-in electric field was driven by the difference of W f . 194 The enhancement of the built-in electric field could not only promote the carrier migration, but also improve the hole collection of the carbon electrode and reduce the charge recombination. 26,195,196
In 2014, Yan et al. found that multi-layer graphene (MG) as a counter electrode would produce a Schottky barrier at the interface with the perovskite layer, which greatly improved the efficiency of the device. 186 Fig. 13(a) and (b) exhibit the energy band diagrams of SG/perovskite and MG/perovskite, respectively. It can be found that there was a large Fermi level shift at the interface between multi-layer graphene and perovskite, forming a Schottky barrier. The MG had some conservative sandwich graphite layers in the oxidation process, so it had a good electrical conductivity. In addition, the mutual accumulation of MG could also fill the defects between each other ( Fig. 13(c) and (d) ). Most importantly, thanks to the built-in field of the Schottky junction, the hole extraction speed was enhanced and the interface charge recombination was greatly suppressed. They achieved a PCE of 11.5%. In 2019, He et al. used copper phthalocyanine (CuPc) to enhance the built-in electric field between the carbon electrode and the perovskite layer, and the efficiency increased to 14.8%. 187 From the SEM images of Fig. 13(f) and (g) , it could be seen that the morphology of the carbon electrode was not affected by CuPc. The device structure with CuPc carbon electrodes is shown in Fig. 13(e) . Compared with the bare carbon electrode, the W f value of the CuPc-doped carbon electrode increased from 4.03 eV to 4.22 eV ( Fig. 13(h) ). The increase in W f difference led to the enhancement of built-in electric field at the interface between carbon electrode and perovskite layer, which improved J SC , V OC and FF values.
In summary, through the latest progress of the four interface engineering of C-PSCs shown above, it can be seen that the effect of eliminating hysteresis is the best, and the other three are achieved by mixing other materials with carbon electrodes. 64,197–202 Obviously, eliminating the hysteresis phenomenon is the most likely to update the highest efficiency of the carbon electrode.
5. Conclusion and outlooks
To further improve the efficiency, the main challenge facing C-PSCs in the future is still the problem of interface contact. This problem stems from the inherent physical properties of carbon materials, e.g. crystal structure, size, electrical conductivity. Simultaneously, the morphology of the perovskite layer also has a great influence on the device. This can be improved through the following strategies. (i) The other materials ( e.g. copper phthalocyanine, MXene) doped with carbon electrodes are used to accelerate charge transfer, enhance charge collection and reduce charge recombination. (ii) The high-quality perovskite films are prepared by a room temperature solvent exchange method, melt-assisted growth method and top seed method to reduce surface defects and improve interfacial contact. (iii) The interlayer ( e.g. copper phthalocyanine and polyethyleneimine-functionalized) is added to the carbon electrode/perovskite interface with improving the work function, reducing the energy level mismatch and increasing the contact area.
The low-temperature carbon electrode discussed in the literature has good interfacial contact and a series of studies can be carried out. These are good research directions. Furthermore, based on the light absorption properties of carbon materials, the development of new characterization methods of C-PSCs is also a very important direction. This can increase the light absorption capacity of carbon materials, resulting in more electron–hole pairs and increased efficiency. Overall, there is much room to enhance their stability and efficiency for future practical applications.
Author contributions
Conflicts of interest, acknowledgements.
- A. Kojima, K. Teshima, Y. Shirai and T. Miyasaka, J. Am. Chem. Soc. , 2009, 131 , 6050–6051 CrossRef CAS PubMed .
- H. S. Kim, C. R. Lee, J. H. Im, K. B. Lee, T. Moehl, A. Marchioro, S. J. Moon, R. Humphry-Baker, J. H. Yum, J. E. Moser, M. Gratzel and N. G. Park, Sci. Rep. , 2012, 2 , 591 CrossRef .
- J. Burschka, N. Pellet, S. J. Moon, R. Humphry-Baker, P. Gao, M. K. Nazeeruddin and M. Gratzel, Nature , 2013, 499 , 316–319 CrossRef CAS PubMed .
- J. H. Im, I. H. Jang, N. Pellet, M. Gratzel and N. G. Park, Nat. Nanotechnol. , 2014, 9 , 927–932 CrossRef CAS PubMed .
- M. Liu, M. B. Johnston and H. J. Snaith, Nature , 2013, 501 , 395–398 CrossRef CAS .
- K. Yan, M. Long, T. Zhang, Z. Wei, H. Chen, S. Yang and J. Xu, J. Am. Chem. Soc. , 2015, 137 , 4460–4468 CrossRef CAS PubMed .
- T. Zhang, X. Meng, Y. Bai, S. Xiao, C. Hu, Y. Yang, H. Chen and S. Yang, J. Mater. Chem. A , 2017, 5 , 1103–1111 RSC .
- G. Xing, N. Mathews, S. Sun, S. S. Lim, Y. M. Lam, M. Gratzel, S. Mhaisalkar and T. C. Sum, Science , 2013, 342 , 344–347 CrossRef CAS .
- D. Shi, V. Adinolfl, R. Comin, M. Yuan, E. Alarousu, A. Buin, Y. Chen, S. Hoogland, A. Rothenberger, K. Katsiev, Y. Losovyj, X. Zhang, P. A. Dowben, O. F. Mohammed, E. H. Sargent and O. M. Bakr, Science , 2015, 347 , 519–522 CrossRef CAS .
- C. S. Ponseca Jr, T. J. Savenije, M. Abdellah, K. Zheng, A. Yartsev, T. Pascher, T. Harlang, P. Chabera, T. Pullerits, A. Stepanov, J. P. Wolf and V. Sundstrom, J. Am. Chem. Soc. , 2014, 136 , 5189–5192 CrossRef .
- K.-G. Lim, S. Ahn, Y.-H. Kim, Y. Qi and T.-W. Lee, Energy Environ. Sci. , 2016, 9 , 932–939 RSC .
- Q. Dong, Y. Fang, Y. Shao, P. Mulligan, J. Qiu, L. Cao and J. Huang, Science , 2015, 347 , 967–970 CrossRef CAS PubMed .
- V. D'Innocenzo, G. Grancini, M. J. Alcocer, A. R. Kandada, S. D. Stranks, M. M. Lee, G. Lanzani, H. J. Snaith and A. Petrozza, Nat. Commun. , 2014, 5 , 3586 CrossRef PubMed .
- S. Y. Sun, T. Salim, N. Mathews, M. Duchamp, C. Boothroyd, G. C. Xing, T. C. Sum and Y. M. Lam, Energy Environ. Sci. , 2014, 7 , 399–407 RSC .
- R. F. Service, Science , 2016, 354 , 1214–1215 CrossRef CAS .
- D. Akin Kara, K. Kara, G. Oylumluoglu, M. Z. Yigit, M. Can, J. J. Kim, E. K. Burnett, D. L. Gonzalez Arellano, S. Buyukcelebi, F. Ozel, O. Usluer, A. L. Briseno and M. Kus, ACS Appl. Mater. Interfaces , 2018, 10 , 30000–30007 CrossRef CAS .
- M. M. Lee, J. Teuscher, T. Miyasaka, T. N. Murakami and H. J. Snaith, Science , 2019, 338 , 643–647 CrossRef .
- Laboratory, N.R.E., 2021, http://www.nrel.
- H. Chen and S. Yang, Adv. Mater. , 2017, 29 , 1603994 CrossRef .
- B. Vaagensmith, K. M. Reza, M. N. Hasan, H. Elbohy, N. Adhikari, A. Dubey, N. Kantack, E. Gaml and Q. Qiao, ACS Appl. Mater. Interfaces , 2017, 9 , 35861–35870 CrossRef CAS .
- G. Martínez-Denegri, S. Colodrero, M. Kramarenko and J. Martorell, ACS Appl. Energy Mater. , 2018, 1 , 5548–5556 Search PubMed .
- M. I. Hossain, A. Hongsingthong, W. Qarony, P. Sichanugrist, M. Konagai, A. Salleo, D. Knipp and Y. H. Tsang, ACS Appl. Mater. Interfaces , 2019, 11 , 14693–14701 CrossRef CAS PubMed .
- I. M. Hossain, D. Hudry, F. Mathies, T. Abzieher, S. Moghadamzadeh, D. Rueda-Delgado, F. Schackmar, M. Bruns, R. Andriessen, T. Aernouts, F. Di Giacomo, U. Lemmer, B. S. Richards, U. W. Paetzold and A. Hadipour, ACS Appl. Energy Mater. , 2018, 2 , 47–58 CrossRef .
- P. Tockhorn, J. Sutter, R. Colom, L. Kegelmann, A. Al-Ashouri, M. Roß, K. Jäger, T. Unold, S. Burger, S. Albrecht and C. Becker, ACS Photonics , 2020, 7 , 2589–2600 CrossRef CAS .
- Z. Ku, Y. Rong, M. Xu, T. Liu and H. Han, Sci. Rep. , 2013, 3 , 3132 CrossRef PubMed .
- F. Zhang, X. Yang, H. Wang, M. Cheng, J. Zhao and L. Sun, ACS Appl. Mater. Interfaces , 2014, 6 , 16140–16146 CrossRef CAS .
- Z. Liu, T. Shi, Z. Tang, B. Sun and G. Liao, Nanoscale , 2016, 8 , 7017–7023 RSC .
- H. Zhang, J. Xiao, J. Shi, H. Su, Y. Luo, D. Li, H. Wu, Y.-B. Cheng and Q. Meng, Adv. Funct. Mater. , 2018, 28 , 1802985 CrossRef .
- H. W. Park, D. U. Lee, M. G. Park, R. Ahmed, M. H. Seo, L. F. Nazar and Z. Chen, ChemSusChem , 2015, 8 , 1058–1065 CrossRef CAS .
- X. Meng, J. Zhou, J. Hou, X. Tao, S. H. Cheung, S. K. So and S. Yang, Adv. Mater. , 2018, 30 , e1706975 CrossRef PubMed .
- M. Chen, R.-H. Zha, Z.-Y. Yuan, Q.-S. Jing, Z.-Y. Huang, X.-K. Yang, S.-M. Yang, X.-H. Zhao, D.-L. Xu and G.-D. Zou, Chem. Eng. J. , 2017, 313 , 791–800 CrossRef CAS .
- C.-H. Lu, G. V. Biesold-McGee, Y. Liu, Z. Kang and Z. Lin, Chem. Soc. Rev. , 2020, 49 , 4953–5007 RSC .
- Z. Zong, B. He, J. Zhu, Y. Ding, W. Zhang, J. Duan, Y. Zhao, H. Chen and Q. Tang, Sol. Energy Mater. Sol. Cells , 2020, 209 , 110460 CrossRef CAS .
- Y. Wang, J. Zhang, S. Chen, H. Zhang, L. Li and Z. Fu, J. Mater. Sci. , 2018, 53 , 9180–9190 CrossRef CAS .
- H. Chen and S. Yang, J. Mater. Chem. A , 2019, 7 , 15476–15490 RSC .
- Y. Yue, N. Salim, Y. Wu, X. Yang, A. Islam, W. Chen, J. Liu, E. Bi, F. Xie, M. Cai and L. Han, Adv. Mater. , 2016, 28 , 10738–10743 CrossRef CAS .
- J. Ryu, K. Lee, J. Yun, H. Yu, J. Lee and J. Jang, Small , 2017, 13 , 1701225 CrossRef PubMed .
- C. Ding, F. Liu, Y. Zhang, D. Hirotani, X. Rin, S. Hayase, T. Minemoto, T. Masuda, R. Wang and Q. Shen, Nano Energy , 2020, 67 , 104267 CrossRef CAS .
- I.-G. Bae and B. Park, Sustainable Energy Fuels , 2020, 4 , 3115–3128 RSC .
- J. Zhu, M. Tang, B. He, W. Zhang, X. Li, Z. Gong, H. Chen, Y. Duan and Q. Tang, J. Mater. Chem. A , 2020, 8 , 20987–20997 RSC .
- X. Lin, D. Cui, X. Luo, C. Zhang, Q. Han, Y. Wang and L. Han, Energy Environ. Sci. , 2020, 13 , 3823–3847 RSC .
- J. A. Raiford, S. T. Oyakhire and S. F. Bent, Energy Environ. Sci. , 2020, 13 , 1997–2023 RSC .
- R. Nie, R. R. Sumukam, S. H. Reddy, M. Banavoth and S. I. Seok, Energy Environ. Sci. , 2020, 13 , 2363–2385 RSC .
- K. D. G. I. Jayawardena, S. M. Silva and R. K. Misra, J. Mater. Chem. C , 2020, 8 , 10641–10675 RSC .
- N. Li, X. Niu, Q. Chen and H. Zhou, Chem. Soc. Rev. , 2020, 49 , 8235–8286 RSC .
- M. Aftabuzzaman, C. Lu and H. K. Kim, Nanoscale , 2020, 12 , 17590–17648 RSC .
- D. Bogachuk, S. Zouhair, K. Wojciechowski, B. Yang, V. Babu, L. Wagner, B. Xu, J. Lim, S. Mastroianni, H. Pettersson, A. Hagfeldt and A. Hinsch, Energy Environ. Sci. , 2020, 13 , 3880–3916 RSC .
- S. Gong, H. Li, Z. Chen, C. Shou, M. Huang and S. Yang, ACS Appl. Mater. Interfaces , 2020, 12 , 34882–34889 CrossRef CAS .
- H. P. Boehm, Carbon , 1994, 13 , 759–769 CrossRef .
- S. K. Hazra, S. Ghosh and T. K. Nandi, Appl. Therm. Eng. , 2019, 163 , 114402 CrossRef CAS .
- N. Cheng, P. Liu, F. Qi, Y. Xiao, W. Yu, Z. Yu, W. Liu, S.-S. Guo and X.-Z. Zhao, J. Power Sources , 2016, 332 , 24–29 CrossRef CAS .
- H. Wei, J. Xiao, Y. Yang, S. Lv, J. Shi, X. Xu, J. Dong, Y. Luo, D. Li and Q. Meng, Carbon , 2015, 93 , 861–868 CrossRef CAS .
- F. R. Li, Y. Xu, W. Chen, S. H. Xie and J. Y. Li, J. Mater. Chem. A , 2017, 5 , 10374–10379 RSC .
- J. H. Im, J. Luo, M. Franckevicius, N. Pellet, P. Gao, T. Moehl, S. M. Zakeeruddin, M. K. Nazeeruddin, M. Gratzel and N. G. Park, Nano Lett. , 2015, 15 , 2120–2126 CrossRef CAS .
- Z. Zhuang, L. Qiu, L. Dong, Y. Chen, Z. Chu, X. Ma, P. Du and J. Xiong, Polym. Compos. , 2020, 41 , 2145–2153 CrossRef CAS .
- Z. Wei, K. Yan, H. Chen, Y. Yi, T. Zhang, X. Long, J. Li, L. Zhang, J. Wang and S. Yang, Energy Environ. Sci. , 2014, 7 , 3326–3333 RSC .
- B. Huang, G. Kong, E. N. Esfahani, S. Chen, Q. Li, J. Yu, N. Xu, Y. Zhang, S. Xie, H. Wen, P. Gao, J. Zhao and J. Li, npj Quantum Mater. , 2018, 3 DOI: 10.1038/s41535-018-0104-5 .
- D. Bai, H. Bian, Z. Jin, H. Wang, L. Meng, Q. Wang and S. Liu, Nano Energy , 2018, 52 , 408–415 CrossRef CAS .
- Y. Guo, X. Yin, J. Liu and W. Que, J. Mater. Chem. A , 2019, 7 , 19008–19016 RSC .
- Z. Wang, X. Liu, Y. Lin, Y. Liao, Q. Wei, H. Chen, J. Qiu, Y. Chen and Y. Zheng, J. Mater. Chem. A , 2019, 7 , 2773–2779 RSC .
- Y. Fan, J. Fang, X. Chang, M.-C. Tang, D. Barrit, Z. Xu, Z. Jiang, J. Wen, H. Zhao, T. Niu, D.-M. Smilgies, S. Jin, Z. Liu, E. Q. Li, A. Amassian, S. Liu and K. Zhao, Joule , 2019, 3 , 2485–2502 CrossRef CAS .
- J. K. Nam, M. S. Jung, S. U. Chai, Y. J. Choi, D. Kim and J. H. Park, J. Phys. Chem. Lett. , 2017, 8 , 2936–2940 CrossRef CAS .
- Q.-Q. Chu, Z. Sun, B. Ding, K.-S. Moon, G.-J. Yang and C.-P. Wong, Nano Energy , 2020, 77 , 105110 CrossRef CAS .
- Z. Wei, H. Chen, K. Yan, X. Zheng and S. Yang, J. Mater. Chem. A , 2015, 3 , 24226–24231 RSC .
- M. Duan, Y. Rong, A. Mei, Y. Hu, Y. Sheng, Y. Guan and H. Han, Carbon , 2017, 120 , 71–76 CrossRef CAS .
- C. Zhang, S. Wang, H. Zhang, Y. Feng, W. Tian, Y. Yan, J. Bian, Y. Wang, S. Jin, S. M. Zakeeruddin, M. Grätzel and Y. Shi, Energy Environ. Sci. , 2019, 12 , 3585–3594 RSC .
- X. Hu, H. Jiang, J. Li, J. Ma, D. Yang, Z. Liu, F. Gao and S. F. Liu, Nanoscale , 2017, 9 , 8274–8280 RSC .
- K. Ahmad and S. M. Mobin, New J. Chem. , 2017, 41 , 14253–14258 RSC .
- J. H. Heo, D. H. Shin, D. H. Song, D. H. Kim, S. J. Lee and S. H. Im, J. Mater. Chem. A , 2018, 6 , 8251–8258 RSC .
- Q.-D. Yang, J. Li, Y. Cheng, H.-W. Li, Z. Guan, B. Yu and S.-W. Tsang, J. Mater. Chem. A , 2017, 5 , 9852–9858 RSC .
- S. Suragtkhuu, O. Tserendavag, U. Vandandoo, A. S. R. Bati, M. Bat-Erdene, J. G. Shapter, M. Batmunkh and S. Davaasambuu, RSC Adv. , 2020, 10 , 9133–9139 RSC .
- V. Babu, R. F. Pineda, T. Ahmad, A. Alvarez, L. A. Castriotta, A. D. Carlo, F. Fabregat-Santiago and K. Wojciechowski, ACS Appl. Energy Mater. , 2020, 3 , 5126–5134 CrossRef CAS .
- P. You, Z. Liu, Q. Tai, S. Liu and F. Yan, Adv. Mater. , 2015, 27 , 3632–3638 CrossRef CAS .
- H. Sung, N. Ahn, M. S. Jang, J.-K. Lee, H. Yoon, N.-G. Park and M. Choi, Adv. Energy Mater. , 2016, 6 , 1501873 CrossRef .
- J. H. Heo, D. H. Shin, S. Kim, M. H. Jang, M. H. Lee, S. W. Seo, S.-H. Choi and S. H. Im, Chem. Eng. J. , 2017, 323 , 153–159 CrossRef CAS .
- R. Ishikawa, S. Watanabe, S. Yamazaki, T. Oya and N. Tsuboi, ACS Appl. Energy Mater. , 2019, 2 , 171–175 CrossRef CAS .
- G. Mazzotta, M. Dollmann, S. N. Habisreutinger, M. G. Christoforo, Z. Wang, H. J. Snaith, M. K. Riede and R. J. Nicholas, ACS Appl. Mater. Interfaces , 2019, 11 , 1185–1191 CrossRef CAS .
- Q. Luo, H. Ma, Q. Hou, Y. Li, J. Ren, X. Dai, Z. Yao, Y. Zhou, L. Xiang, H. Du, H. He, N. Wang, K. Jiang, H. Lin, H. Zhang and Z. Guo, Adv. Funct. Mater. , 2018, 28 , 1706777 CrossRef .
- I. Jeon, A. Shawky, S. Seo, Y. Qian, A. Anisimov, E. I. Kauppinen, Y. Matsuo and S. Maruyama, J. Mater. Chem. A , 2020, 8 , 11141–11147 RSC .
- R. Wu, Q. Luo, L. Ma, C. Wang, H. Liu, H. Lin, N. Wang, Y. Chen and Z. Guo, Adv. Funct. Mater. , 2020, 31 , 2004765 Search PubMed .
- M. K. A. Mohammed, RSC Adv. , 2020, 10 , 35831–35839 RSC .
- S. Seo, I. Jeon, R. Xiang, C. Lee, H. Zhang, T. Tanaka, J.-W. Lee, D. Suh, T. Ogamoto, R. Nishikubo, A. Saeki, S. Chiashi, J. Shiomi, H. Kataura, H. M. Lee, Y. Yang, Y. Matsuo and S. Maruyama, J. Mater. Chem. A , 2019, 7 , 12987–12992 RSC .
- X. Wu, L. Xie, K. Lin, J. Lu, K. Wang, W. Feng, B. Fan, P. Yin and Z. Wei, J. Mater. Chem. A , 2019, 7 , 12236–12243 RSC .
- N. Ahn, I. Jeon, J. Yoon, E. I. Kauppinen, Y. Matsuo, S. Maruyama and M. Choi, J. Mater. Chem. A , 2018, 6 , 1382–1389 RSC .
- Q. Luo, H. Ma, Y. Zhang, X. Yin, Z. Yao, N. Wang, J. Li, S. Fan, K. Jiang and H. Lin, J. Mater. Chem. A , 2016, 4 , 5569–5577 RSC .
- R. B. K. Siram, M. V. Khenkin, A. Niazov-Elkan, K. M. Anoop, H. Weissman, E. A. Katz, I. Visoly-Fisher and B. Rybtchinski, Nanoscale , 2019, 11 , 3733–3740 RSC .
- R. Belchi, B. Pibaleau, M. Pinault, B. Ratier, N. Herlin-Boime and J. Bouclé, Mater. Adv. , 2020, 1 , 1232–1240 RSC .
- C. Ma, S. Clark, Z. Liu, L. Liang, Y. Firdaus, R. Tao, A. Han, X. Liu, L. J. Li, T. D. Anthopoulos, M. C. Hersam and T. Wu, ACS Nano , 2020, 14 , 3969–3979 CrossRef CAS PubMed .
- Q. Luo, H. Ma, F. Hao, Q. Hou, J. Ren, L. Wu, Z. Yao, Y. Zhou, N. Wang, K. Jiang, H. Lin and Z. Guo, Adv. Funct. Mater. , 2017, 27 , 1703068 CrossRef .
- K. Aitola, K. Sveinbjörnsson, J.-P. Correa-Baena, A. Kaskela, A. Abate, Y. Tian, E. M. J. Johansson, M. Grätzel, E. I. Kauppinen, A. Hagfeldt and G. Boschloo, Energy Environ. Sci. , 2016, 9 , 461–466 RSC .
- H. Zhou, Q. Chen, G. Li, S. Luo, T.-B. Song, H.-S. Duan, Z. Hong, J. You, Y. Liu and Y. Yang, Science , 2017, 345 , 542–546 CrossRef PubMed .
- J. H. N. W. S. Yang, N. J. Jeon, Y. C. Kim, J. S. S. Ryu and S. Il Seok, Science , 2018, 348 , 1234–1237 CrossRef PubMed .
- M. Saliba, K. Domanski, J.-Y. Seo, A. Ummadisingu, S. M. Zakeeruddin, J.-P. Correa-Baena, W. R. Tress, A. Abate, A. Hagfeldt and M. Grätzel, Science , 2018, 354 , 206–209 CrossRef PubMed .
- W. S. Yang, E. H. Jung, N. J. Jeon, Y. C. Kim, D. U. Lee, S. S. Shin, J. Seo, E. K. Kim, J. H. Noh and S. Il Seok, Science , 2017, 356 , 1376–1379 CrossRef CAS .
- N. J. Jeon, H. Na, E. H. Jung, T.-Y. Yang, Y. G. Lee, G. Kim, H.-W. Shin, S. Il Seok, J. Lee and J. Seo, Nat. Energy , 2018, 3 , 682–689 CrossRef CAS .
- Q. Jiang, Y. Zhao, X. Zhang, X. Yang, Y. Chen, Z. Chu, Q. Ye, X. Li, Z. Yin and J. You, Nat. Photonics , 2019, 13 , 460–466 CrossRef CAS .
- J. J. Yoo, G. Seo, M. R. Chua, T. G. Park, Y. Lu, F. Rotermund, Y. K. Kim, C. S. Moon, N. J. Jeon, J. P. Correa-Baena, V. Bulovic, S. S. Shin, M. G. Bawendi and J. Seo, Nature , 2021, 590 , 587–593 CrossRef CAS .
- A. Mei, X. Li, L. Liu, Z. Ku, T. Liu, Y. Rong, M. Xu, M. Hu, J. Chen, Y. Yang, M. Gratzel and H. Han, Science , 2014, 345 , 295–298 CrossRef CAS PubMed .
- Y. Yang, K. Ri, A. Mei, L. Liu, M. Hu, T. Liu, X. Li and H. Han, J. Mater. Chem. A , 2015, 3 , 9103–9107 RSC .
- J. Chen, Y. Xiong, Y. Rong, A. Mei, Y. Sheng, P. Jiang, Y. Hu, X. Li and H. Han, Nano Energy , 2016, 27 , 130–137 CrossRef CAS .
- H. Zhang, H. Wang, S. T. Williams, D. Xiong, W. Zhang, C. C. Chueh, W. Chen and A. K. Jen, Adv. Mater. , 2017, 29 , 1606608 CrossRef PubMed .
- S. Shukla, T. M. Koh, R. Patidar, J. H. Lew, P. Kajal, S. G. Mhaisalkar and N. Mathews, J. Phys. Chem. C , 2021, 125 , 6585–6592 CrossRef CAS .
- Z. Wei, H. Chen, K. Yan and S. Yang, Angew. Chem., Int. Ed. , 2014, 53 , 13239–13243 CrossRef CAS PubMed .
- X. Zheng, H. Chen, Q. Li, Y. Yang, Z. Wei, Y. Bai, Y. Qiu, D. Zhou, K. S. Wong and S. Yang, Nano Lett. , 2017, 17 , 2496–2505 CrossRef CAS PubMed .
- Y. Yang, Z. Liu, W. K. Ng, L. Zhang, H. Zhang, X. Meng, Y. Bai, S. Xiao, T. Zhang, C. Hu, K. S. Wong and S. Yang, Adv. Funct. Mater. , 2019, 29 , 1806506 CrossRef .
- H. Chen, Z. Wei, H. He, X. Zheng, K. S. Wong and S. Yang, Adv. Energy Mater. , 2016, 6 , 1502087 CrossRef .
- K. Lee, J. Kim, H. Yu, J. W. Lee, C.-M. Yoon, S. K. Kim and J. Jang, J. Mater. Chem. A , 2018, 6 , 24560–24568 RSC .
- S. Wang, P. Jiang, W. Shen, A. Mei, S. Xiong, X. Jiang, Y. Rong, Y. Tang, Y. Hu and H. Han, Chem. Commun. , 2019, 55 , 2765–2768 RSC .
- Y. Cao, W. Li, Z. Liu, Z. Zhao, Z. Xiao, W. Zi and N. Cheng, J. Mater. Chem. A , 2020, 8 , 12080–12088 RSC .
- P. Mariani, L. Najafi, G. Bianca, M. I. Zappia, L. Gabatel, A. Agresti, S. Pescetelli, A. Di Carlo, S. Bellani and F. Bonaccorso, ACS Appl. Mater. Interfaces , 2021, 13 , 22368–22380 CrossRef CAS PubMed .
- Y. Rong, Z. Ku, A. Mei, T. Liu, M. Xu, S. Ko, X. Li and H. Han, J. Phys. Chem. Lett. , 2014, 5 , 2160–2164 CrossRef CAS PubMed .
- L. Zhang, T. Liu, L. Liu, M. Hu, Y. Yang, A. Mei and H. Han, J. Mater. Chem. A , 2015, 3 , 9165–9170 RSC .
- M. Xu, Y. Rong, Z. Ku, A. Mei, T. Liu, L. Zhang, X. Li and H. Han, J. Mater. Chem. A , 2014, 2 , 8607–8611 RSC .
- A. K. Baranwal, S. Kanaya, T. A. Peiris, G. Mizuta, T. Nishina, H. Kanda, T. Miyasaka, H. Segawa and S. Ito, ChemSusChem , 2016, 9 , 2604–2608 CrossRef CAS PubMed .
- E. V. Péan, C. S. De Castro, S. Dimitrov, F. De Rossi, S. Meroni, J. Baker, T. Watson and M. L. Davies, Adv. Funct. Mater. , 2020, 30 , 1909839 CrossRef .
- S. Wang, W. Shen, Y. Chu, W. Zhang, L. Hong, A. Mei, Y. Rong, Y. Tang, Y. Hu and H. Han, J. Phys. Chem. Lett. , 2020, 11 , 9689–9695 CrossRef CAS PubMed .
- R. Kerremans, O. J. Sandberg, S. Meroni, T. Watson, A. Armin and P. Meredith, Sol. RRL , 2019, 4 , 1900221 CrossRef .
- J. Baker, K. Hooper, S. Meroni, A. Pockett, J. McGettrick, Z. Wei, R. Escalante, G. Oskam, M. Carnie and T. Watson, J. Mater. Chem. A , 2017, 5 , 18643–18650 RSC .
- D. Raptis, V. Stoichkov, S. M. P. Meroni, A. Pockett, C. A. Worsley, M. Carnie, D. A. Worsley and T. Watson, Curr. Appl. Phys. , 2020, 20 , 619–627 CrossRef .
- A. Pockett, D. Raptis, S. M. P. Meroni, J. Baker, T. Watson and M. Carnie, J. Phys. Chem. C , 2019, 123 , 11414–11421 CrossRef CAS .
- D. Papadatos, D. Sygkridou and E. Stathatos, Mater. Lett. , 2020, 268 , 127621 CrossRef CAS .
- J. Ryu, S. Yoon, J. Park, S. M. Jeong and D.-W. Kang, Appl. Surf. Sci. , 2020, 516 , 146116 CrossRef CAS .
- T. Ye, X. Jiang, D. Wan, X. Wang, J. Xing, T. Venkatesan, Q. Xiong and S. Ramakrishna, Chem. Phys. Chem. , 2016, 17 , 4102–4109 CrossRef CAS PubMed .
- I. Onwubiko, W. S. Khan, B. Subeshan and R. Asmatulu, Energy Ecol. Environ. , 2020, 5 , 141–152 CrossRef .
- Q.-Q. Chu, B. Ding, Y. Li, L. L. Gao, Q. Qiu, C.-X. Li, C.-J. Li, G.-J. Yang and B. Fang, ACS Sustainable Chem. Eng. , 2017, 5 , 9758–9765 CrossRef CAS .
- Y. Wang, H. Zhao, Y. Mei, H. Liu, S. Wang and X. Li, ACS Appl. Mater. Interfaces , 2019, 11 , 916–923 CrossRef CAS PubMed .
- H. Chen and S. Yang, J. Mater. Res. , 2017, 32 , 3011–3020 CrossRef CAS .
- Y. Yang, J. Xiao, H. Wei, L. Zhu, D. Li, Y. Luo, H. Wu and Q. Meng, RSC Adv. , 2014, 4 , 52825–52830 RSC .
- C. Lee, S.-W. Lee, S. Bae, A. Shawky, V. Devaraj, A. Anisimov, E. I. Kauppinen, J.-W. Oh, Y. Kang, D. Kim, I. Jeon, S. Maruyama and H.-S. Lee, Sol. RRL , 2020, 4 , 2000353 CrossRef CAS .
- I. Jeon, J. Yoon, U. Kim, C. Lee, R. Xiang, A. Shawky, J. Xi, J. Byeon, H. M. Lee, M. Choi, S. Maruyama and Y. Matsuo, Adv. Energy Mater. , 2019, 9 , 1901204 CrossRef .
- Z. Wei, X. Zheng, H. Chen, X. Long, Z. Wang and S. Yang, J. Mater. Chem. A , 2015, 3 , 16430–16434 RSC .
- Y. Hu, Z. Zhang, A. Mei, Y. Jiang, X. Hou, Q. Wang, K. Du, Y. Rong, Y. Zhou, G. Xu and H. Han, Adv. Mater. , 2018, 30 , 1705786 CrossRef PubMed .
- S.-H. Turren-Cruz, M. Saliba, M. T. Mayer, H. Juárez-Santiesteban, X. Mathew, L. Nienhaus, W. Tress, M. P. Erodici, M.-J. Sher, M. G. Bawendi, M. Grätzel, A. Abate, A. Hagfeldt and J.-P. Correa-Baena, Energy Environ. Sci. , 2018, 11 , 78–86 RSC .
- M. Batmunkh, T. J. Macdonald, C. J. Shearer, M. Bat-Erdene, Y. Wang, M. J. Biggs, I. P. Parkin, T. Nann and J. G. Shapter, Adv. Sci. , 2017, 4 , 1600504 CrossRef PubMed .
- F. Tan, M. I. Saidaminov, H. Tan, J. Z. Fan, Y. Wang, S. Yue, X. Wang, Z. Shen, S. Li, J. Kim, Y. Gao, G. Yue, R. Liu, Z. Huang, C. Dong, X. Hu, W. Zhang, Z. Wang, S. Qu, Z. Wang and E. H. Sargent, Adv. Funct. Mater. , 2020, 30 , 2005155 CrossRef CAS .
- F. Deng, X. Sun, X. Lv, Y. Li and X. Tao, J. Power Sources , 2021, 489 , 229345 CrossRef CAS .
- M. Duan, C. Tian, Y. Hu, A. Mei, Y. Rong, Y. Xiong, M. Xu, Y. Sheng, P. Jiang, X. Hou, X. Zhu, F. Qin and H. Han, ACS Appl. Mater. Interfaces , 2017, 9 , 31721–31727 CrossRef CAS PubMed .
- Y. Sheng, A. Mei, S. Liu, M. Duan, P. Jiang, C. Tian, Y. Xiong, Y. Rong, H. Han and Y. Hu, J. Mater. Chem. A , 2018, 6 , 2360–2364 RSC .
- F. Zhang, X. Yang, M. Cheng, J. Li, W. Wang, H. Wang and L. Sun, J. Mater. Chem. A , 2015, 3 , 24272–24280 RSC .
- Y. Xiong, Y. Liu, K. Lan, A. Mei, Y. Sheng, D. Zhao and H. Han, New J. Chem. , 2018, 42 , 2669–2674 RSC .
- Y. Rong, X. Hou, Y. Hu, A. Mei, L. Liu, P. Wang and H. Han, Nat. Commun. , 2017, 8 , 14555 CrossRef PubMed .
- C. Raminafshar, V. Dracopoulos, M. R. Mohammadi and P. Lianos, Electrochim. Acta , 2018, 276 , 261–267 CrossRef CAS .
- X. Xu, Z. Liu, Z. Zuo, M. Zhang, Z. Zhao, Y. Shen, H. Zhou, Q. Chen, Y. Yang and M. Wang, Nano Lett. , 2015, 15 , 2402–2408 CrossRef CAS PubMed .
- C. Tian, A. Mei, S. Zhang, H. Tian, S. Liu, F. Qin, Y. Xiong, Y. Rong, Y. Hu, Y. Zhou, S. Xie and H. Han, Nano Energy , 2018, 53 , 160–167 CrossRef CAS .
- H. Tao, Y. Li, C. Zhang, K. Wang, J. Wang, B. Tan, L. Han and J. Tao, Solid State Commun. , 2018, 271 , 71–75 CrossRef CAS .
- F. Behrouznejad, C. M. Tsai, S. Narra, E. W. Diau and N. Taghavinia, ACS Appl. Mater. Interfaces , 2017, 9 , 25204–25215 CrossRef CAS PubMed .
- P. Jiang, Y. Xiong, M. Xu, A. Mei, Y. Sheng, L. Hong, T. W. Jones, G. J. Wilson, S. Xiong, D. Li, Y. Hu, Y. Rong and H. Han, J. Phys. Chem. C , 2018, 122 , 16481–16487 CrossRef CAS .
- F. Zhang, X. Yang, M. Cheng, W. Wang and L. Sun, Nano Energy , 2016, 20 , 108–116 CrossRef CAS .
- R. Hu, R. Zhang, Y. Ma, W. Liu, L. Chu, W. Mao, J. Zhang, J. Yang, Y. Pu and X. A. Li, Appl. Surf. Sci. , 2018, 462 , 840–846 CrossRef CAS .
- H. Ye, Z. Liu, X. Liu, B. Sun, X. Tan, Y. Tu, T. Shi, Z. Tang and G. Liao, Appl. Surf. Sci. , 2019, 478 , 417–425 CrossRef CAS .
- H. Liu, X. Fu, W. Fu, B. Zong, L. Huang, H. Bala, S. Wang, Z. Guo, G. Sun, J. Cao and Z. Zhang, Org. Electron. , 2018, 59 , 253–259 CrossRef CAS .
- J. Chen and N.-G. Park, ACS Energy Lett. , 2020, 5 , 2742–2786 CrossRef CAS .
- A. Bashir, S. Shukla, J. H. Lew, S. Shukla, A. Bruno, D. Gupta, T. Baikie, R. Patidar, Z. Akhter, A. Priyadarshi, N. Mathews and S. G. Mhaisalkar, Nanoscale , 2018, 10 , 2341–2350 RSC .
- R. L. Davidovich, V. Stavila, D. V. Marinin, E. I. Voit and K. H. Whitmire, Coord. Chem. Rev. , 2009, 253 , 1316–1352 CrossRef CAS .
- G. Mahmoudi, A. Bauza and A. Frontera, Dalton Trans. , 2016, 45 , 4965–4969 RSC .
- K. Dasgupta and D. Sathiyamoorthy, Mater. Sci. Technol. , 2013, 19 , 995–1002 CrossRef .
- S. Stankovich, D. A. Dikin, R. D. Piner, K. A. Kohlhaas, A. Kleinhammes, Y. Jia, Y. Wu, S. T. Nguyen and R. S. Ruoff, Carbon , 2007, 45 , 1558–1565 CrossRef CAS .
- S.-S. Li, K.-H. Tu, C.-C. Lin, C.-W. Chen and M. Chhowalla, ACS Nano , 2010, 4 , 3169–3174 CrossRef CAS PubMed .
- C. Mattevi, G. Eda, S. Agnoli, S. Miller, K. A. Mkhoyan, O. Celik, D. Mastrogiovanni, G. Granozzi, E. Garfunkel and M. Chhowalla, Adv. Funct. Mater. , 2009, 19 , 2577–2583 CrossRef CAS .
- H. S. Kim and N. G. Park, J. Phys. Chem. Lett. , 2014, 5 , 2927–2934 CrossRef CAS PubMed .
- W. Tress, J. P. Correa Baena, M. Saliba, A. Abate and M. Graetzel, Adv. Energy Mater. , 2016, 6 , 1600396 CrossRef .
- C. Xia, W.-D. Song, C.-Z. Zhang, S.-Y. Yuan, W.-X. Hu, P. Qin, R.-P. Wang, L.-L. Zhao, X.-F. Wang, M. He and S.-T. Li, Chin. Phys. B , 2017, 26 , 018401 CrossRef .
- M. F. Ayguler, A. G. Hufnagel, P. Rieder, M. Wussler, W. Jaegermann, T. Bein, V. Dyakonov, M. L. Petrus, A. Baumann and P. Docampo, ACS Appl. Mater. Interfaces , 2018, 10 , 11414–11419 CrossRef PubMed .
- J. Y. Kim, J. W. Lee, H. S. Jung, H. Shin and N. G. Park, Chem. Rev. , 2020, 120 , 7867–7918 CrossRef CAS PubMed .
- S. Mashhoun, Y. Hou, H. Chen, F. Tajabadi, N. Taghavinia, H.-J. Egelhaaf and C. J. Brabec, Adv. Energy Mater. , 2018, 8 , 1802085 CrossRef .
- L. Fagiolari and F. Bella, Energy Environ. Sci. , 2019, 12 , 3437–3472 RSC .
- B. Chen, M. Yang, S. Priya and K. Zhu, J. Phys. Chem. Lett. , 2016, 7 , 905–917 CrossRef CAS PubMed .
- S. N. Habisreutinger, N. K. Noel and H. J. Snaith, ACS Energy Lett. , 2018, 3 , 2472–2476 CrossRef CAS .
- P. Calado, A. M. Telford, D. Bryant, X. Li, J. Nelson, B. C. O'Regan and P. R. Barnes, Nat. Commun. , 2016, 7 , 13831 CrossRef CAS PubMed .
- Y. Zhou, F. Huang, Y.-B. Cheng and A. Gray-Weale, Comput. Mater. Sci. , 2017, 126 , 22–28 CrossRef CAS .
- S. Ravishankar, S. Gharibzadeh, C. Roldán-Carmona, G. Grancini, Y. Lee, M. Ralaiarisoa, A. M. Asiri, N. Koch, J. Bisquert and M. K. Nazeeruddin, Joule , 2018, 2 , 788–798 CrossRef CAS .
- S. A. L. Weber, I. M. Hermes, S.-H. Turren-Cruz, C. Gort, V. W. Bergmann, L. Gilson, A. Hagfeldt, M. Graetzel, W. Tress and R. Berger, Energy Environ. Sci. , 2018, 11 , 2404–2413 RSC .
- H. J. Snaith, A. Abate, J. M. Ball, G. E. Eperon, T. Leijtens, N. K. Noel, S. D. Stranks, J. T. Wang, K. Wojciechowski and W. Zhang, J. Phys. Chem. Lett. , 2014, 5 , 1511–1515 CrossRef CAS PubMed .
- J. Park, S. E. Yoon, J. Lee, D. R. Whang, S. Y. Lee, S. J. Shin, J. M. Han, H. Seo, H. J. Park, J. H. Kim and B. G. Kim, Adv. Funct. Mater. , 2020, 30 , 2001560 CrossRef CAS .
- X. Wang, L. Zhi and K. Mullen, Nano Lett. , 2008, 8 , 323–327 CrossRef CAS PubMed .
- L. G. De Arco, Y. Zhang, C. W. Schlenker, K. Ryu, M. E. Thompson and C. Zhou, ACS Nano , 2010, 4 , 2865–2873 CrossRef PubMed .
- H. Park, P. R. Brown, V. Bulović and J. Kong, Nano Lett. , 2011, 12 , 133–140 CrossRef PubMed .
- Z. Yin, J. Zhu, Q. He, X. Cao, C. Tan, H. Chen, Q. Yan and H. Zhang, Adv. Energy Mater. , 2014, 4 , 1300574 CrossRef .
- R. Singh, P. K. Singh, B. Bhattacharya and H.-W. Rhee, Appl. Mater. Today , 2019, 14 , 175–200 CrossRef .
- G. Huang, C. Wang, H. Zhang, S. Xu, Q. Xu and Y. Cui, J. Mater. Chem. A , 2018, 6 , 2449–2455 RSC .
- Y. Yang, H. Chen, C. Hu and S. Yang, J. Mater. Chem. A , 2019, 7 , 22005–22011 RSC .
- S. Liu, L. Guan, T. Zhang, X. Gong, X. Zhao, Q. Sun, X. Shai, X. L. Zhang, X. Xiao, Y. Shen and M. Wang, Appl. Mater. Today , 2020, 20 , 100644 CrossRef .
- M. Abd Mutalib, F. Aziz, A. F. Ismail, W. N. Wan Salleh, N. Yusof, J. Jaafar, T. Soga, M. Z. Sahdan and N. Ahmad Ludin, Appl. Mater. Today , 2018, 13 , 69–82 CrossRef .
- M.-y. Li, H. Yin and G.-Y. Sun, Appl. Mater. Today , 2020, 21 , 100799 CrossRef .
- W. Chidawanyika and T. Nyokong, Carbon , 2010, 48 , 2831–2838 CrossRef CAS .
- K. Yan, Z. Wei, J. Li, H. Chen, Y. Yi, X. Zheng, X. Long, Z. Wang, J. Wang, J. Xu and S. Yang, Small , 2015, 11 , 2269–2274 CrossRef CAS PubMed .
- S. He, L. Qiu, D.-Y. Son, Z. Liu, E. J. Juarez-Perez, L. K. Ono, C. Stecker and Y. Qi, ACS Energy Lett. , 2019, 4 , 2032–2039 CrossRef CAS .
- O. J. Sandberg, J. Kurpiers, M. Stolterfoht, D. Neher, P. Meredith, S. Shoaee and A. Armin, Adv. Mater. Interfaces , 2020, 7 , 2000041 CrossRef CAS .
- http://www.bookshop.unsw.edu.au .
- W. A. Laban and L. Etgar, Energy Environ. Sci. , 2013, 6 , 3249–3253 RSC .
- L. Cai, Y. Wang, N. Li, A. A. Syed and F. Zhu, Energy Technol. , 2020, 8 , 2000192 CrossRef CAS .
- J. Wu, Y. Li, S. Tan, B. Yu, H. Li, Y. Li, J. Shi, H. Wu, Y. Luo, D. Li and Q. Meng, ACS Appl. Mater. Interfaces , 2020, 12 , 27258–27267 CrossRef CAS PubMed .
- H. Chen and S. Yang, Sci. Bull. , 2016, 61 , 1680–1688 CrossRef CAS .
- J.-H. Lee, J. Kim, G. Kim, D. Shin, S. Y. Jeong, J. Lee, S. Hong, J. W. Choi, C.-L. Lee, H. Kim, Y. Yi and K. Lee, Energy Environ. Sci. , 2018, 11 , 1742–1751 RSC .
- Z. Liu, X. Yu and L. Li, Chin. J. Catal. , 2020, 41 , 534–549 CrossRef CAS .
- W. T. Wang, P. Chen, C. H. Chiang, T. F. Guo, C. G. Wu and S. P. Feng, Adv. Funct. Mater. , 2020, 30 , 1909755 CrossRef CAS .
- B. Fan, T. You, K. Wang, R. Yin, Y. Gao, L. Huo and P. Yin, ACS Appl. Energy Mater. , 2021, 4 , 5821–5829 CrossRef CAS .
- W. Zhu, Q. Zhang, C. Zhang, Z. Zhang, D. Chen, Z. Lin, J. Chang, J. Zhang and Y. Hao, ACS Appl. Energy Mater. , 2018, 1 , 4991–4997 CrossRef CAS .
- J. Li, J. Duan, J. Du, X. Yang, Y. Wang, P. Yang, Y. Duan and Q. Tang, ACS Appl. Mater. Interfaces , 2020, 12 , 47408–47415 CrossRef CAS PubMed .
- K. Wang, Z. Zhang, L. Wang, K. Chen, L. Tao, Y. Zhang and X. Zhou, ACS Appl. Energy Mater. , 2021, 4 , 3255–3264 CrossRef CAS .
- E. Calabro, F. Matteocci, B. Paci, L. Cina, L. Vesce, J. Barichello, A. Generosi, A. Reale and A. Di Carlo, ACS Appl. Mater. Interfaces , 2020, 12 , 32536–32547 CrossRef CAS PubMed .
- W. Chai, J. Ma, W. Zhu, D. Chen, H. Xi, J. Zhang, C. Zhang and Y. Hao, ACS Appl. Mater. Interfaces , 2021, 13 , 2868–2878 CrossRef CAS PubMed .

IMAGES
VIDEO
COMMENTS
Thesis: Ph. D., Massachusetts Institute of Technology, Department of Chemistry, May, 2020. Cataloged from the official PDF of thesis. ... The post treatment of the bulk perovskite thin film with 2D perovskites via SPD strategy prevented formation of a detrimental non-perovskite phase at the interface and resulted in much improved thin film ...
THESIS ACCEPTANCE DATE: June 10, 2022 STUDENT'S NAME: LI Yang THESIS TITLE: Design and Synthesis of Perovskite Materials for Photocatalytic and Photovoltaic Applications This is to certify that the above student's thesis has been examined by the following panel ... done after registration for the degree of PhD at Hong Kong Baptist University,
supporting me to pursue my PhD degree. They have provided valuable advice and guidance to help me achieve the goals of my research project even when they have busy schedules. They are always there to offer me support when I have problems and difficulties in my PhD research period. Their motivation and
In this thesis, efficient solar cells and color sensors are studied based on metal-halide perovskite materials. Charge transport/contact layers have a significant impact on the electrical and ...
Perovskite solar cells are predicted to be low-cost because of its low material and fabrication costs, while the efficiency and stability still require further development. This dissertation focused on the efficiency and operation stability enhancement of OIHP solar cell by controlling the OIHP film fabrication process, interfacial layers ...
Perovskite solar cells offer outstanding promise in the world of next-generation renewable energy to help pave the way for a cleaner, greener, and more sustainable future. This PhD thesis addresses two critical challenges currently facing perovskite solar cells: replacing the expensive gold electrode with a scalable and low-cost alternative and improving the operational stability of flexible ...
A dissertation submitted to the faculty at the University of North Carolina at Chapel Hill ... perovskite precursor solution to stabilize the black phase of CsPbI 3. In Chapter 6, a novel phenomenon, self-doping in MAPbI 3 perovskite, was demonstrated and reported. MAPbI 3
Stable Perovskite Solar Cells Ziru Huang Doctor of Philosophy The Edward S. Rogers Sr. Department of Electrical and Computer Engineering University of Toronto 2021 ... The completion of this thesis is due to the constructive suggestions and support I received from many people. I thank my friends, colleagues, and my family for helping me. ...
Student thesis: Doctoral Thesis › PhD. ... Perovskite solar cells have shown extraordinary performance, reaching power conversion efficiencies of over 24% in less than a decade. Some of the reasons for their success are the high light absorption and the possibility of using low cost solution-based fabrication. Perovskite devices are notably ...
PHD Characterization of Perovskite Solar Cells Pockett, Adam Award date: 2017 Awarding institution: University of Bath ... This thesis may be made available for consultation within the University Library and ... been transferred to the study of planar perovskite devices. These include impedance spectroscopy (EIS), intensity modulated ...
Thesis for: PhD; Advisor: Alexander Zakhidov, Luisa Scolfaro, Todd Hudnall, Shane Yost, Amanda Neukirch; ... Regions detailing perovskite solar cells are highlighted and enlarged. ...
PEROVSKITE BASED SOLAR CELL DEVICES IN STANDALONE AND TANDEM CONFIGURATION By KHAGENDRA PRASAD PHULARA Supervised By PROF. DR. SALVATORE FAVA A DISSERTATION Presented to the SELINUS UNIVERSITY OF SCIENCE AND LITERATURE Faculty of ENGINEERING AND TECHNOLOGY In fulfillment of the requirements for the degree of Doctor of Philosophy 2022
Here, a photodetector based on SC-TF perovskite active layer is reported with a record performance of a 50 million gain, 70 GHz gain-bandwidth product, and a 100-photon level detection limit at ...
The work presented in this thesis will describe studies on organic-inorganic perovskite materials when being used in tandem and multi-junction solar cell architectures. Perovskite solar cells (PSC) have recently emerged as a viable absorber material for photovoltaic applications, owing to its remarkable optoelectronic properties along with its ...
PEROVSKITE SOLAR CELL FOR GREENHOUSE APPLICATIONS LINDA YEN-CHIEN CHEN MPhil, University of Auckland, 2014 A thesis submitted in partial fulfilment of the requirements for the degree of DOCTOR OF PHILOSOPHY In ELECTRICAL AND COMPUTER ENGINEERING Department of Electrical and Computer Engineering
In the final part of this thesis, multi-bandgap perovskite materials are considered for the realization of efficient vertically stacked colorsensors. The vertically stacked color sensor consists of three different energy bandgap perovskite diodes (channels), which allows exhibiting excellent color separation without having any color aliasing or ...
Noora Lamminen: Development of antimony-based perovskite-inspired solar cells Master of Science Thesis Tampere University Materials Science and Engineering January 2022 One of the most important challenges to ght climate change is nding alternative clean energy production methods. In just more than a decade, perovskite has become the most ...
University of Texas at El Paso
Sining Yun received his PhD in 2007 working on perovskite oxides at Xi'an Jiaotong University, China. He joined Xi'an University of Architecture and Technology in 2007 as an assistant professor. After a postdoctoral program (2008-2009) working on dye-sensitized solar cells at Yonsei University (Korea), he has been an associate professor ...
Abstract and Figures. Ph.D. thesis. Stability is one of the key points for real world application of solar cells and is mainly related to the processes that regulate the energy conversion, both in ...
PDF | This is a literature Thesis made by Master student Aram Farawar on Perovskites. It may be usefull for anyone interested in the field. | Find, read and cite all the research you need on ...
Metal-halide perovskite based solar cells have now achieved a light to electricity conversion efficiency of 26.1%, making them the leading emerging thin-film solar cell material. Read more. Supervisor: Dr J Patel. 1 July 2024 PhD Research Project Funded PhD Project (Students Worldwide) More Details.
Perovskite based oxide, PhD Thesis, Goa University, 2010. https://bit.ly/2JnThNh. CHAPTER 2 . STRUCTURE OF PEROVSKITES . Introduction-The Perovskite Structure. The perovskite has general formula ...